LEITERPLATTEN-VERBINDER: VERGLEICH ZWISCHEN LITZEN- UND FLEX-VERBINDUNG
(English version see below)
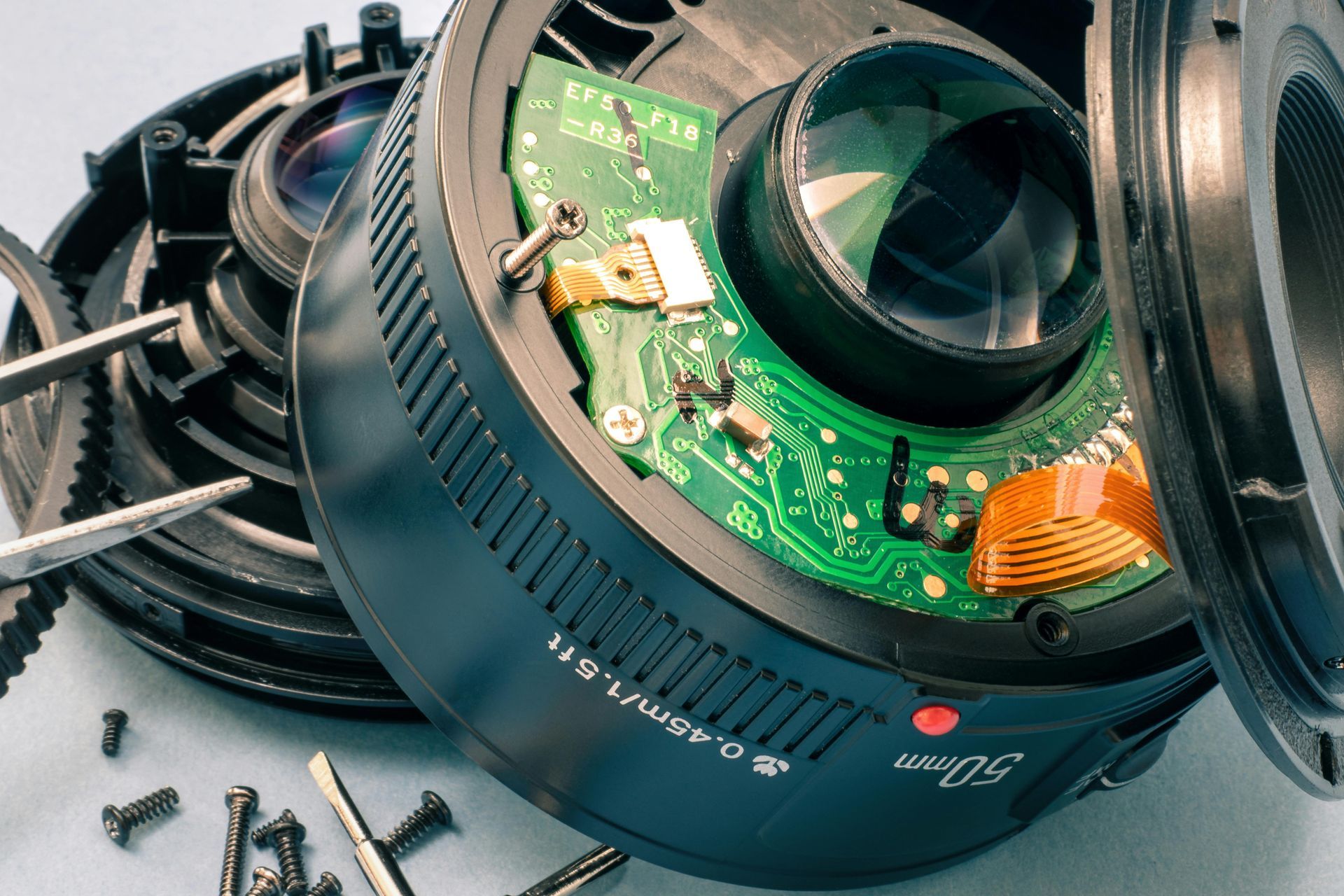
Der Artikel von John Brunt (Harwin Plc) beleuchtet die Unterschiede zwischen Litzen- und Flex-Verbindung (semi-flex, starr-flex, flex; englisch: FPC = Flexible Printed Circuits) und gibt wertvolle Hinweise zur Auswahl der geeigneten Lösung.
Wichtige Überlegungen:
1) Stromstärken: Flex-Verbindungen sind prinzipiell dünner, um die Biegemöglichkeit sicherzustellen. Hier ist mit einer Grenze zu rechnen, bis die Flexibilität der Flex-Verbindung aufgehoben wird. Diese Grenze schränkt auch die Strombelastbarkeit der Flex-Verbindung ein, während diskrete Drähte höhere Ströme unterstützen können.
Ein weiterer Faktor, die der Strombelastbarkeit bestimmt, ist die Wärmeableitung, denn bei hohem Stromfluss entsteht Wärme. Wird prinzipiell die Stromverbindung zu warm, kann davon das Isolationsmaterial geschädigt werden und das die Zuverlässigkeit einschränken. Hier bestimmt die Packungsdichte oder Verlegung der (Flex-) Leitung, wie die Wärme abgeleitet werden kann.
Da die Flex-Verbindung fest mit der Leiterplatte verbunden ist, kann sie nicht schnell geändert werden. Muss während des (Muster-)Aufbaus schnell die Strombelastbarkeit geändert werden, ist die Litzen-Verbindung von Vorteil.
2) Gewicht und Platz: Flex-Verbindungen sind ideal für Anwendungen mit strengen Gewichtsbeschränkungen, wie z.B. UAVs (Unmanned Aerial Vehicel/Unbemanntes Luftfahrzeug), da sie weniger Platz benötigen und leichter sind. Der rechteckige Querschnitt einer Flex-Verbindung im Vergleich zu einem runden Querschnitt der Leitung macht es möglich, in einer Dimension kompakter zu bauen.
Der Aufbau einer Flex-Verbindung verbindet meist alle Leitungen parallel nebeneinander. Außerdem sind sie meist in einem Verbund zusammengefasst, der sie optimal zueinander führt. Dies vereinfacht die Montage, wenn über eine längere Distanz die Leitungen im Gerät verlegt werden. Einzelne Litzen müssen eventuell zusätzlich geführt werden, während der Flex-Verbund immer zuverlässig eine Lage im Gehäuse einnimmt. Dies kann Zeit und Kosten bei der Montage der Flex-Verbindung einsparen.
Ein weiterer Aspekt einer Litzenverbindung ist die Notwendigkeit einer Klemme oder eines Steckers zur Anbindung an die Leiterplatte. Dieser zusätzliche Platzbedarf fällt bei einer Flex-Verbindung weg, da sie direkt bei der Pressung einer Flex-Leiterplatte eingebaut wird. Lediglich bei einseitigen Flex-Verbindungen, bei denen an der anderen Kontaktseite mit einem flachen Steckverbinder gearbeitet wird, entsteht Platz- und Montagebedarf.
3) Biegung und Flexibilität: Flex-Verbindungen ermöglichen engere Biegungen, sind jedoch nur in einer Richtung flexibel. Diskrete Drähte können in allen Dimensionen gebogen oder verdrillt werden, was einen größeren Handlungsspielraum bei der Geräte-Konstruktion ermöglichen kann.
Es muss bei der Wahl der elektrischen Verbindung unterschieden werden, ob die flexible Verbindung nur einmalig zur Montage oder auch während des Betriebs benötigt wird. Außerdem kann durch externe mechanische Einflüsse die elektrische Verbindung während dem Betrieb belastet werden. Hier sind für einzelne Leitungen hochwertige Mantelwerkstoffe verfügbar, die „schleppketten-fähig“ sind, was eine ständige intensive Biegebelastung der elektrischen Verbindung bedeutet. Je nach Einsatzfall kann hier die Flex-Verbindung als Möglichkeit wegfallen.
###
English version:
PRINTED CIRCUIT BOARD CONNECTORS: COMPARISON BETWEEN STRANDED AND FLEX CONNECTIONS
John Brunt’s (Harwin Plc) article highlights the differences between stranded and flex connections (semi-flex, rigid-flex, flex; FPC = Flexible Printed Circuits) and provides valuable information on choosing the right solution.
Important considerations:
1) Current ratings: Flex connections are generally thinner to ensure that they can be bent. A limit must be expected here until the flexibility of the flex connection is removed. This limit also restricts the current carrying capacity of the flex connection, whereas discrete wires can support higher currents.
Another factor that determines the current-carrying capacity is heat dissipation, as heat is generated when the current flow is high. In principle, if the power connection becomes too warm, the insulation material can be damaged and this can limit reliability. The packing density or routing of the (flex) cable determines how the heat can be dissipated.
As the flex connection is permanently connected to the PCB, it cannot be changed quickly. If the current carrying capacity needs to be changed quickly during (sample) assembly, the stranded wire connection has an advantage.
2) Weight and space: Flex connections are ideal for applications with strict weight restrictions, such as UAVs (Unmanned Aerial Vehicles), as they take up less space and are lighter. The rectangular cross-section of a flex connection compared to a round cross-section of the cable makes it possible to build more compactly in one dimension.
The structure of a flex connection usually connects all cables in parallel next to each other. In addition, they are usually grouped together in a compound that guides them optimally to each other. This simplifies installation if the cables are laid over a longer distance in the device. The individual strands may have to be routed additionally, while the flex composite always reliably occupies one position in the housing. This can save time and costs when installing the flex connection.
Another aspect of a stranded wire connection is the need for a terminal or connector to connect it to the PCB. This additional space requirement is eliminated with a flex connection, as it is installed directly when a flex PCB is pressed. Only single-sided flex connections, where a flat connector is used on the other contact side, require additional space and assembly.
3) Bending and flexibility: Flex connections allow for tighter bends, but are only flexible in one direction. Discrete wires can be bent or twisted in all dimensions, which can allow greater flexibility in device design.
When selecting the electrical connection, a distinction must be made as to whether the flexible connection is only required once for installation or also during operation. In addition, external mechanical influences can stress the electrical connection during operation. High-quality sheath materials are available for individual cables that are "drag chain-capable", which means that the electrical connection is subject to constant intensive bending stress. Depending on the application, the flex connection may not be an option here.
4) Environmental conditions: The choice of material is crucial, especially in harsh environments, to ensure the longevity of the connections. Here, the quality of the individual cables can usually be the better choice. There are high-quality sheath materials that are resistant to high temperatures, moisture, oil, UV, fungi or cleaning agents. If the electrical connection is laid outside an enclosure, a flex connection can rarely be selected here.
For further details see article in „Elektronik“ (11, 31.5.2023): https://www.elektroniknet.de/e-mechanik-passive/verbindungstechnik/hi-rel-systeme-sicher-verbinden.205618.html
Wichtige Überlegungen:
1) Stromstärken: Flex-Verbindungen sind prinzipiell dünner, um die Biegemöglichkeit sicherzustellen. Hier ist mit einer Grenze zu rechnen, bis die Flexibilität der Flex-Verbindung aufgehoben wird. Diese Grenze schränkt auch die Strombelastbarkeit der Flex-Verbindung ein, während diskrete Drähte höhere Ströme unterstützen können.
Ein weiterer Faktor, die der Strombelastbarkeit bestimmt, ist die Wärmeableitung, denn bei hohem Stromfluss entsteht Wärme. Wird prinzipiell die Stromverbindung zu warm, kann davon das Isolationsmaterial geschädigt werden und das die Zuverlässigkeit einschränken. Hier bestimmt die Packungsdichte oder Verlegung der (Flex-) Leitung, wie die Wärme abgeleitet werden kann.
Da die Flex-Verbindung fest mit der Leiterplatte verbunden ist, kann sie nicht schnell geändert werden. Muss während des (Muster-)Aufbaus schnell die Strombelastbarkeit geändert werden, ist die Litzen-Verbindung von Vorteil.
2) Gewicht und Platz: Flex-Verbindungen sind ideal für Anwendungen mit strengen Gewichtsbeschränkungen, wie z.B. UAVs (Unmanned Aerial Vehicel/Unbemanntes Luftfahrzeug), da sie weniger Platz benötigen und leichter sind. Der rechteckige Querschnitt einer Flex-Verbindung im Vergleich zu einem runden Querschnitt der Leitung macht es möglich, in einer Dimension kompakter zu bauen.
Der Aufbau einer Flex-Verbindung verbindet meist alle Leitungen parallel nebeneinander. Außerdem sind sie meist in einem Verbund zusammengefasst, der sie optimal zueinander führt. Dies vereinfacht die Montage, wenn über eine längere Distanz die Leitungen im Gerät verlegt werden. Einzelne Litzen müssen eventuell zusätzlich geführt werden, während der Flex-Verbund immer zuverlässig eine Lage im Gehäuse einnimmt. Dies kann Zeit und Kosten bei der Montage der Flex-Verbindung einsparen.
Ein weiterer Aspekt einer Litzenverbindung ist die Notwendigkeit einer Klemme oder eines Steckers zur Anbindung an die Leiterplatte. Dieser zusätzliche Platzbedarf fällt bei einer Flex-Verbindung weg, da sie direkt bei der Pressung einer Flex-Leiterplatte eingebaut wird. Lediglich bei einseitigen Flex-Verbindungen, bei denen an der anderen Kontaktseite mit einem flachen Steckverbinder gearbeitet wird, entsteht Platz- und Montagebedarf.
3) Biegung und Flexibilität: Flex-Verbindungen ermöglichen engere Biegungen, sind jedoch nur in einer Richtung flexibel. Diskrete Drähte können in allen Dimensionen gebogen oder verdrillt werden, was einen größeren Handlungsspielraum bei der Geräte-Konstruktion ermöglichen kann.
Es muss bei der Wahl der elektrischen Verbindung unterschieden werden, ob die flexible Verbindung nur einmalig zur Montage oder auch während des Betriebs benötigt wird. Außerdem kann durch externe mechanische Einflüsse die elektrische Verbindung während dem Betrieb belastet werden. Hier sind für einzelne Leitungen hochwertige Mantelwerkstoffe verfügbar, die „schleppketten-fähig“ sind, was eine ständige intensive Biegebelastung der elektrischen Verbindung bedeutet. Je nach Einsatzfall kann hier die Flex-Verbindung als Möglichkeit wegfallen.
4) Umgebungsbedingungen:
Die Wahl des Materials ist entscheidend, insbesondere in harschen Umgebungen, um die Langlebigkeit der Verbindungen zu gewährleisten. Hier kann meist die Qualität der einzelnen Leitungen die bessere Wahl sein. Es existieren hochwertige Mantelwerkstoffe, die hochtemperatur-, feuchtigkeits, öl-, UV-, pilz- oder reinigungsmittelbeständig sind. Bei Verlegung der elektrischen Verbindung außerhalb eines Gehäuses kann hier selten eine Flex-Verbindung gewählt werden.
->
Möchten Sie in einem Projekt eine Flex-Variante einsetzen und benötigen Beratung zur Umsetzung? Dann kontaktieren sie gerne MDI: 0176/29243030
oder sb@elektronikkonstrukteur.de
Zum Weiterlesen siehe Artikel in „Elektronik“ (11, 31.5.2023): https://www.elektroniknet.de/e-mechanik-passive/verbindungstechnik/hi-rel-systeme-sicher-verbinden.205618.html
###
English version:
PRINTED CIRCUIT BOARD CONNECTORS: COMPARISON BETWEEN STRANDED AND FLEX CONNECTIONS
John Brunt’s (Harwin Plc) article highlights the differences between stranded and flex connections (semi-flex, rigid-flex, flex; FPC = Flexible Printed Circuits) and provides valuable information on choosing the right solution.
Important considerations:
1) Current ratings: Flex connections are generally thinner to ensure that they can be bent. A limit must be expected here until the flexibility of the flex connection is removed. This limit also restricts the current carrying capacity of the flex connection, whereas discrete wires can support higher currents.
Another factor that determines the current-carrying capacity is heat dissipation, as heat is generated when the current flow is high. In principle, if the power connection becomes too warm, the insulation material can be damaged and this can limit reliability. The packing density or routing of the (flex) cable determines how the heat can be dissipated.
As the flex connection is permanently connected to the PCB, it cannot be changed quickly. If the current carrying capacity needs to be changed quickly during (sample) assembly, the stranded wire connection has an advantage.
2) Weight and space: Flex connections are ideal for applications with strict weight restrictions, such as UAVs (Unmanned Aerial Vehicles), as they take up less space and are lighter. The rectangular cross-section of a flex connection compared to a round cross-section of the cable makes it possible to build more compactly in one dimension.
The structure of a flex connection usually connects all cables in parallel next to each other. In addition, they are usually grouped together in a compound that guides them optimally to each other. This simplifies installation if the cables are laid over a longer distance in the device. The individual strands may have to be routed additionally, while the flex composite always reliably occupies one position in the housing. This can save time and costs when installing the flex connection.
Another aspect of a stranded wire connection is the need for a terminal or connector to connect it to the PCB. This additional space requirement is eliminated with a flex connection, as it is installed directly when a flex PCB is pressed. Only single-sided flex connections, where a flat connector is used on the other contact side, require additional space and assembly.
3) Bending and flexibility: Flex connections allow for tighter bends, but are only flexible in one direction. Discrete wires can be bent or twisted in all dimensions, which can allow greater flexibility in device design.
When selecting the electrical connection, a distinction must be made as to whether the flexible connection is only required once for installation or also during operation. In addition, external mechanical influences can stress the electrical connection during operation. High-quality sheath materials are available for individual cables that are "drag chain-capable", which means that the electrical connection is subject to constant intensive bending stress. Depending on the application, the flex connection may not be an option here.
4) Environmental conditions: The choice of material is crucial, especially in harsh environments, to ensure the longevity of the connections. Here, the quality of the individual cables can usually be the better choice. There are high-quality sheath materials that are resistant to high temperatures, moisture, oil, UV, fungi or cleaning agents. If the electrical connection is laid outside an enclosure, a flex connection can rarely be selected here.
For further details see article in „Elektronik“ (11, 31.5.2023): https://www.elektroniknet.de/e-mechanik-passive/verbindungstechnik/hi-rel-systeme-sicher-verbinden.205618.html
Ein Bildschirm mit einem Durchmesser von weniger als 0,5 mm verfügt über 14.000 Pixel pro Zoll - unfassbare Zahlen. Das proprietäre Eye-Tracking-System übertrifft durch reine Bewegungssensoren und algorithmische Verarbeitung jede bestehende optische Lösung. Dies verändert alles, wie wir mit Computern umgehen. BAHNBRECHENDE SPEZIFIKATIONEN: 15-Grad-Sichtfeld Verfolgung in Echtzeit Pixelabstand unter 2 Mikrometer Kontinuierliche Akkulaufzeit von 2 Stunden Die Anforderungen an den Halscomputer mögen einschränkend erscheinen. In Wirklichkeit eröffnet sie Möglichkeiten, die über die traditionellen Beschränkungen der Datenverarbeitung hinausgehen. MARKTREALITÄTEN: $205 Millionen an Finanzmitteln 110 engagierte Mitarbeiter 5 Jahre Zeitplan für die Kommerzialisierung (ab 2022) Erste medizinische Anwendungen im Fokus Die Implikationen gehen weit über die einfache Display-Technologie hinaus. Es handelt sich um die nächste große Computerplattform. Erste Herausforderungen müssen gelöst werden: mechatronische Integration in einem sehr empfindlichen Körperbereich Optimierung der Batterielebensdauer Medizinische Zulassung Größenordnung der Massenproduktion ❗️ABER: Leider: Nur ein Jahr später, 2023, wurde das Projekt auf unbestimmte Zeit verschoben, weil das Geld für weitere Forschungen fehlte. TROTZDEM: Was denken Sie über diese Art von Innovation? Wären Sie daran interessiert, sie zu nutzen? Quellen: https://youtu.be/A6aGDBp8Yl4 , https://mixed-news.com/en/ar-contact-lens-mojo-vision-unveils-new-prototype/ ; https://mixed.de/ar-kontaktlinsen-von-mojo-vision-auf-eis-gelegt-fokus-auf-microled/ Bilder: https://mixed-news.com/en/ar-contact-lens-mojo-vision-unveils-new-prototype/ ; AI software
> Die Optimierung der Produktionseffizienz bietet unmittelbare Möglichkeiten für einen ökologischen Fortschritt. Durch den Einsatz fortschrittlicher Methoden des Widerstandspunktschweißens kann der Energieverbrauch in den Produktionsprozessen gesenkt werden.
>
>
> > Zusätzlich ermöglicht die Einführung der Clip- und Schraubmethode anstelle des Klebens eine Kostensenkung und eine verbesserte Effizienz der Montagelinie.
>
> > Das Lebenszyklusmanagement von Batterien stellt eine transformative Entwicklung bei Nachhaltigkeitsinitiativen dar. Die Industrie geht von traditionellen linearen Verbrauchsmodellen zu dienstleistungsbasierten Lösungen über. Zu den aktuellen Marktimplementierungen gehören Tausch- und Pfandsysteme, die das Paradigma der Batterienutzung grundlegend umgestalten.
>
> Die aktuellen Fortschritte in der Materialwissenschaft bieten bedeutende Chancen. Unsere Forschungs- und Entwicklungsbemühungen konzentrieren sich auf innovative Verbundwerkstoffe, die das Potenzial haben, das Design von Bat
ZUVERLÄSSIGKEIT ist in der Medizintechnik nicht optional - sie ist sehr wichtig.
Entwickelst Du Geräte mit Steckverbindern, Leiterplattenklemmen, flache Steckanschlüsse und andere Verbindungselemente in der Medizintechnik?
Hier sind die Themen, die in der Verbindungstechnologie in medizinischen Geräten enorm wichtig sind:
Lebenskritische Operationen:
- Kontinuierliche Funktionalität ist nicht verhandelbar
- Jede Komponente muss die ZERO-FAIL-Leistung beibehalten
- Standards wie IEC 60601-1 gewährleisten strenge Sicherheitsprotokolle
Umweltherausforderungen:
- Resistenz gegen Reinigungsmittel und medizinische Gase
- Schutz vor Kontamination
- Temperaturstabilität unter extremen Bedingungen
Operative Anforderungen:
- 24/7/365 Funktionalität erforderlich
- Keine Redundanz in kritischen Systemen
- Null-Toleranz für Verbindungsfehler
Investitionsschutz:
- Medizinische Einrichtungen investieren stark in Ausrüstung
- Langfristige Zuverlässigkeit wirkt sich auf den ROI aus
- Die Komponentenqualität wirkt si
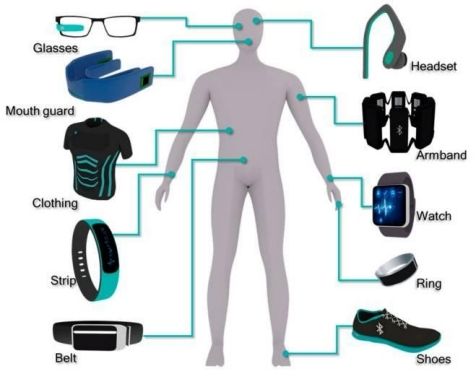
Wearables entwickeln sich weiter: Von einfachen Fitness-Trackern zu intelligenten Geräten, die unseren Körper verstehen und vorhersagen können, was wir brauchen. 👉 Bist Du als Konstrukteur darauf vorbereitet? Kennst Du die Gehäuse-Technologien, die dazu nötig sind? Diese Schlüsselentwicklungen sind gerade im Kommen: - Nahtlose Integration: Fortschrittliche Geräte interpretieren jetzt physiologische Signale mit medizinischer Präzision - Individuelle Intelligenz: Systeme analysieren personalisierte Datenmuster für individuelle Erkenntnisse - Vorausschauende Fähigkeiten: Maschinelles Lernen ermöglicht vorausschauende Antworten auf Benutzerbedürfnisse Kritische Herausforderungen : - Energieeffizienz - Sensorgenauigkeit - Datenanalyse Der Paradigmenwechsel liegt in der nahtlosen Integration der Technologie mit der menschlichen Erfahrung, die sich von externen Werkzeugen zu biologischen Erweiterungen verwandelt. #WearableTech #Innovation #FutureTech #TechEvolution #DigitalTransformation Quelle: https://med.stanford.edu/snyderlab/news/2022-our-wearable-future--part-1--what-will-new-tech-look-like--.html
Wissen durch Projekte oder gezielte Weiterbildung?
Viele Konstrukteure in der Elektromechanik/Mechatronik lernen projektgetrieben.
Das dauert aber sehr lange, gefährdet Projektpläne und kann viel Geld kosten.
Wichtig zu wissen: Der Konstrukteur muss kein Elektronik-Wissen erlernen. Er muss seinen Handlungsspielraum mit der Elektronik kennen und kann damit das Gehäuse robust auslegen.
Selecting the right PCB spacers requires careful consideration of various factors, including the importance of spacers, the different types and applications, and material selection. By following these three top tips, you can ensure that your electronic assemblies are reliable, functional and durable.

Die Messe „Embedded World“ fand vom 09.-11.04.2024 in Nürnberg statt und ist nun vorüber. Viele Elektronik- und Software- Highlights wurden vorgestellt. Einen guten Überblick findest Du hier über Tag 1 , Tag 2 und Tag 3 . Du fragst Dich vielleicht, was hat nun die embedded mit einem Konstrukteur zu tun? Die Antwort gibt Hr. Bernd Hense in seinem Bericht “Impulse” aus der Fachzeitschrift "Elektronik" 07 vom 2.4.2024: Schwerpunkt-Themen der Messe sind hauptsächlich in der Elektronik und Software zu finden. Aber es gibt auch Mechanik-Themen: Anforderungen an die Konstruktion kommen aus der Hochfrequenztechnik: "Zunehmend mehr mobile Geräte, die mit der Umwelt drahtlos kommunizieren, zunehmend mehr äußere Signale wahrnehmen und bei kleiner Bauform möglichst lange laufen sollen. [..] EMV-verträgliches Design ..“ 👍Also spannende Herausforderungen für jeden Konstrukteur👍 → weißt Du, was HF = Hochfrequenz beim Gehäusedesign bedeutet? → weißt Du, was EMV bedeutet? → wie fit bist Du darin, ein möglichst EMV-gerechtes Gehäuse zu entwickeln? → weißt Du, das EMV-verträgliches Design ein Skill ist, der speziell in Jobanzeigen gesucht wird? Du kannst Dich mit dem Wissen über HF und EMV herausheben und spannende und zukunftsfähige Jobs bekommen. → Kennst Du die konstruktiven Möglichkeiten, wie ein möglichst kleines Gerät möglichst lange betrieben werden kann? Schreib mir Deine Antworten gerne an mich: sb@elektronikkonstrukteur.de Ich freue mich über jede Antwort :) Herzliche Grüße Steffen Braun
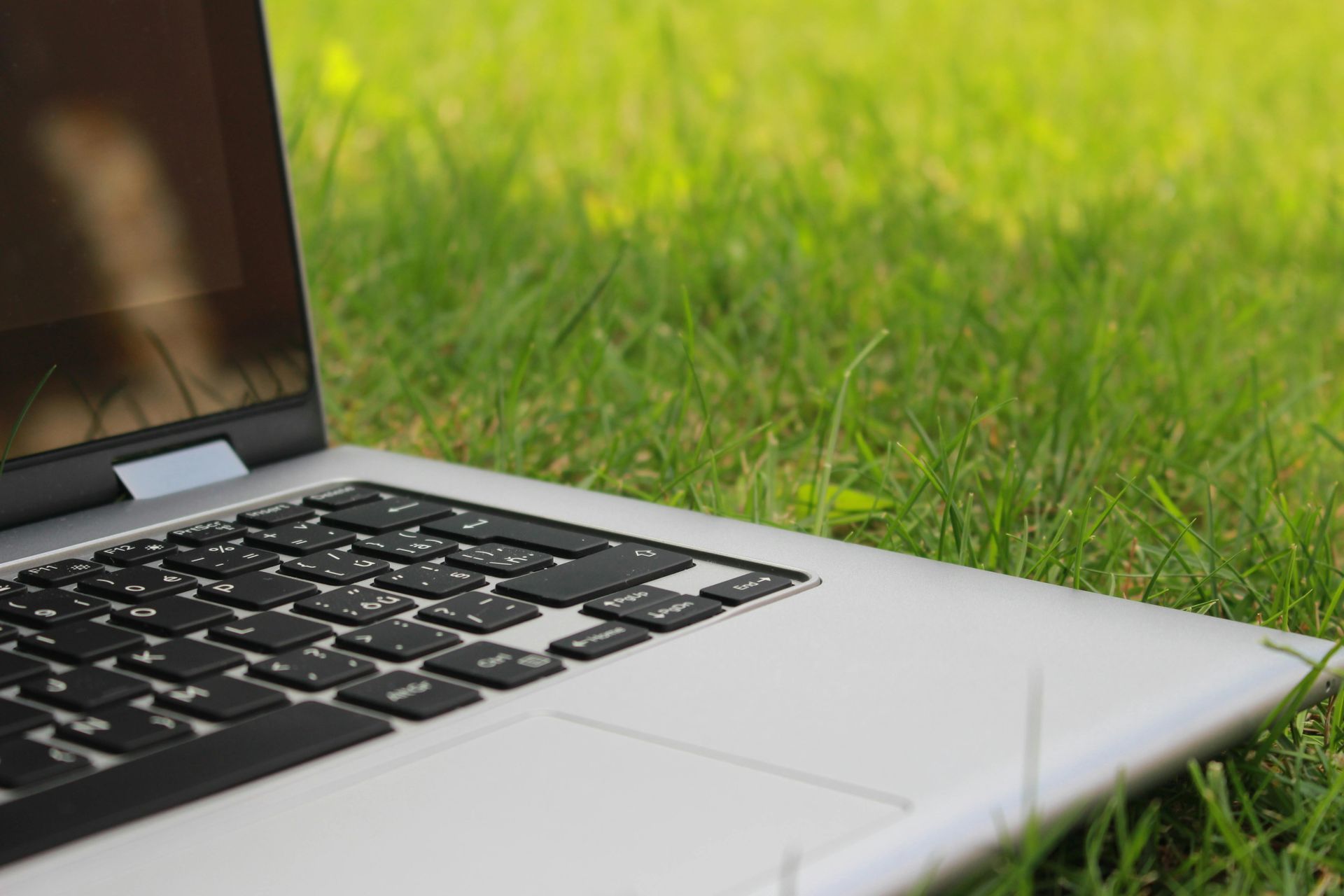
Wir als Produktentwickler haben viel mehr in Hand als wir denken - besonders, wenn es um die Nachhaltigkeit der Produkte geht. Obwohl die Themen “Elektronikschrott” oder “Energieverbrauch von Elektronik” schon lange in den (technischen) Medien behandelt werden, gibt es nun speziell für den Produktentwickler von elektrischen oder elektronischen Produkten Möglichkeiten, die Nachhaltigkeit der Produkte zu steuern.